SEDOT-JOIST STEEL
- J Jayanthi Chandran
- May 15, 2024
- 25 min read
Updated: Aug 28, 2024

The following terms shall, for the purposes of this Specification, have the meanings shown in this Section. Where terms are not defined in this Section, those terms shall have their ordinary accepted meanings in the context in which it applies. Joist Girders, K-Series, LH-Series, and DLH-Series shall be open web, in-plane load-carrying steel members utilizing hotrolled or cold-formed steel, including cold-formed steel whose yield strength has been attained by cold working. Joist Girders shall be open web steel trusses used as primary framing members designed as simple spans supporting inplane concentrated loads for a floor or roof system. These concentrated loads shall be considered to act at the top chord panel points of the Joist Girders unless otherwise specified.
The Joist Girder standard designation in ASD shall be established by its nominal depth in inches (mm), the letter “G”, followed by the number of joist spaces, the letter “N”, the load in kips (kN) at each panel point, and the letter “K”. The Joist Girder standard designation in LRFD shall be established by its nominal depth in inches (mm), the letter “G”, followed by the number of joist spaces, the letter “N”, the factored load in kips (kN) at each panel point, and the letter “F”. Joist Girders shall be designed in accordance with this Specification to support the loads defined by the specifying professional. Joist Girders shall be designed and manufactured as either simple framing members with underslung ends and bottom chord extensions or as part of an ordinary steel moment frame (OMF). Where used as part of an OMF the specifying professional shall be responsible for carrying out all the required frame analyses (i.e. first-order and second-order), provide all the required load information and stiffness data to the joist manufacturer, and indicate the type of Joist Girder to column connections that are being designed on the structural drawings.
User Note: Joist Girders have been standardized in depths from 20 inches (508 mm) through 120 inches (3048 mm), for spans from 20 feet (6096 mm) through 120 feet (36576 mm). Where this Specification refers to “steel joists”, this shall mean the K-Series, LH-Series, and DLH-Series joists. User Note: Joists are suitable for the direct support of floors and roof slabs or decks.
The K-Series joists are standardized in depths from 10 inches (254 mm) through 30 inches (762 mm), for spans up through 60 feet (18288 mm). The LH-Series joists are standardized in depths from 18 inches (457 mm) through 48 inches (1219 mm), for spans up through 96 feet (29261 mm). The DLH-Series joists are standardized in depths from 52 inches (1321 mm) through 120 inches (3048 mm), for spans up through 240 feet (73152 mm). The K-Series, LH-Series and DLH-Series standard joist designations shall be established by their nominal depth, followed by the letters K, LH or DLH as appropriate, and then by the Section Number designation assigned
. The Section Number designations shall range from 01 to 25. The K-Series, LH-Series and DLH-Series standard joist designations listed in the following Standard Load Tables shall support the uniformly distributed loads as provided in the applicable tables: Standard LRFD Load Table Open Web Steel Joists, K-Series – U.S. Customary Units Standard ASD Load Table Open Web Steel Joists, K-Series – U.S. Customary Units Standard LRFD Load Table Longspan Steel Joists, LH-Series – U.S. Customary Units Standard ASD Load Table Longspan Steel Joists, LH-Series – U.S. Customary Units Standard LRFD Load Table Deep Longspan Steel Joists, DLH-Series – U.S. Customary Units Standard ASD Load Table Deep Longspan Steel Joists, DLH-Series – U.S. Customary Units Standard LRFD Load Table Open Web Steel Joists, K-Series – S.I. Units Standard ASD Load Table Open Web Steel Joists, K-Series – S.I. Units Standard LRFD Load Table Longspan Steel Joists, LH-Series – S.I. Units Standard ASD Load Table Longspan Steel Joists, LH-Series – S.I. Units Standard LRFD Load Table Deep Longspan Steel Joists, DLH-Series – S.I. Units Standard ASD Load Table Deep Longspan Steel Joists, DLH-Series – S.I. Units Wherever a standard SJI Section Number is specified in the joist designation (e.g. 18K4, 32LH10) and other design load cases are also specified for the joist, the steel joist shall be designed for the corresponding total load as shown in the Standard Load Tables as a minimum.
The Joist Substitutes, K-Series standard designations are determined by their nominal depth, i.e. 2.5, followed by the letter “K” and then by the chord size designation assigned. The chord size designations range from 1 to 3. Therefore, as a performance based specification, the Joist Substitutes, K-Series standard designations listed in the following Load Tables shall support the uniformly distributed loads as provided in the appropriate tables: LRFD Simple Span Load Table for 2.5 Inch K-Series Joist Substitutes – U.S. Customary Units ASD Simple Span Load Table for 2.5 Inch K-Series Joist Substitutes – U.S. Customary Units LRFD Outriggers Load Table for 2.5 Inch K–Series Joist Substitutes – U.S. Customary Units ASD Outriggers Load Table for 2.5 Inch K–Series Joist Substitutes – U.S. Customary Units And the following Load Tables published electronically at www.steeljoist.org/loadtables LRFD Simple Span Load Table for 64 mm K-Series Joist Substitutes – S.I. Units ASD Simple Span Load Table for 64 mm K-Series Joist Substitutes – S.I. Units LRFD Outriggers Load Table for 64 mm K-Series Joist Substitutes – S.I. Units ASD Outriggers Load Table for 64 mm K-Series Joist Substitutes – S.I. Units A Top Chord Extension or Extended End, K-Series, shall be a joist accessory that shall be designed in accordance with this Specification to support uniform loads when one or both ends of an underslung joist needs to be cantilevered beyond its bearing seat.
The Top Chord Extensions and Extended Ends, K-Series have been standardized as an “S” Type (top chord angles extended only) and an “R” Type (top chord and bearing seat angles extended), respectively. The maximum total safe uniformly distributed load-carrying capacity of either an “R” or “S” Type extension is 550 plf (8.02 kN/m) in ASD or 825 plf (12.03 kN/m) in LRFD. Standard designations for the “S” Type range from S1 to S12 for spans from 0’-6” to 4’-6” (152 to 1372 mm). Standard designations for the “R” Type range from R1 to R12 for spans from 0’-6” to 6’-0” (152 to 1829 mm). Therefore, as a performance based specification, the “S” Type Top Chord Extensions and “R” Type Extended Ends listed in the following Standard Load Tables shall support the uniformly distributed loads as provided in the appropriate tables: LRFD Top Chord Extension Load Table (S Type) – U.S. Customary Units ASD Top Chord Extension Load Table (S Type) – U.S. Customary Units 23 American National Standard SJI-K-2010 Introduction General Joist Information Economical Design Guide Top Chord Ext., K-Series Joist Substitutes & Outriggers KCS Joists Joist LRFD Load Tables Joist ASD Load Tables Load/Load Weight Tables Joist Girder Weight Tables Specifications SJI Standard SJI Code of Stand. Practice Fire Resistance Ratings OSHA Safety Standards www.newmill.com/digital-tools Discover the easiest way to specify steel joists and Joist Girders: 129 SJI Standard Specifications – K-Series 25 American National Standard SJI-K-2010 LRFD Top Chord Extension Load Table (R Type) – U.S. Customary Units ASD Top Chord Extension Load Table (R Type) – U.S. Customary Units And the following Standard Load Tables published electronically at www.steeljoist.org/loadtables LRFD Top Chord Extension Load Table (S Type) – S.I. Units ASD Top Chord Extension Load Table (S Type) – S.I. Units LRFD Top Chord Extension Load Table (R Type) – S.I. Units
K-SERIES Open Web Steel Joists or K-series are defined as simply supported uniformly loaded trusses that can support a floor or roof deck (see Figure 1). The top chord of the joist is assumably braced against lateral buckling by the deck. The K-series is distinguished by the depth range of 8” to 30” with a maximum span of up to 60’ and standard seat depth of 21 /2”. Maximum uniform load for K-series joists is 550 plf. The standard load table found in the Steel Joist Institute Specification uses standard designations which define the joist depth, a series designation, the total load capacity, live load capacity based on L/360 allowable deflection, erection stability bridging requirements and approximate joist weight. It also includes the K-series economy table so the lightest joist for a given load can easily be selected. The ends of K-series joists must extend at least 2 ½” over steel supports (see Figure 2). The KCS joist is a K-series joist developed to allow the building designer to easily specify a standard joist to support not only uniform loads but also concentrated loads or other non-uniform loads.
KCS joist chords are designed for constant moment capacity at all interior panels. All webs are designed for a vertical shear equal to the shear capacity. In addition, all webs (except the first tension web, which remains in tension under all simple span gravity loads) will be designed for 100 % stress reversal. The building designer will calculate the maximum moment and maximum shear and select the appropriate KCS joist from the KCS joist load tables. If a KCS joist cannot be selected, or if any uniform load exceeds 550plf or any concentrated load exceeds the shear capacity of the joist, double KCS joists can be used, or an LH-series joist can be selected.
LH-Series Joists have been standardized in depths from 18 inches (457 mm) through 48 inches (1219 mm), for spans through 96 feet (29,260 mm).
DLH-Series Joists have been standardized in depths from 52 inches (1321 mm) through 120 inches (3048 mm), for spans up through 240 feet (73,152 mm). LH-Series and DLH-Series Steel Joists can be furnished with either under-slung or square ends, with parallel chords or with single or double pitched top chords to provide sufficient slope for roof drainage. Square end joists are primarily intended for bottom chord bearing. Sloped parallel-chord joists shall use span as defined by the length along the slope.
The joist designation is determined by its nominal depth at the center of the span and by the chord size designation. The depth of the bearing seat at the ends of underslung LH-Series and DLH-Series Joists has been established at 5 inches (127 mm) for chord section number 2 through 17. A bearing seat depth of 7 1/2 inches (191 mm) has been established for the DLH-Series Joists chord section number 18 through 25. Open Web Steel Joists are manufactured with standardized camber as given in Section 4.6. For the proper handling of concern
trated and/or varying loads, see Section 2.4 in the Code of Standard Practice for Steel Joists and Joist Girders.
K Series bar joists are designed for use typically with lighter loads and are most common in roof design. K Joists are used typically where shorter span conditions are required.
LH-Series joists are capable of supporting larger loads and are typically used where longer spans and special profiles (such as gable joists and arched joists) are needed in varying conditions. Nominal Dimensions. To learn more, including loading capacity information, please refer to our Technical Information
The LH-Series joists arestandardized in depths from 18 inches (457 mm) through 48 inches (1219 mm), for spans up through 96 feet (29261 mm). The DLH-Series joists are standardized in depths from 52 inches (1321 mm) through 120 inches (3048 mm), for spans up through 240 feet (73152 mm).




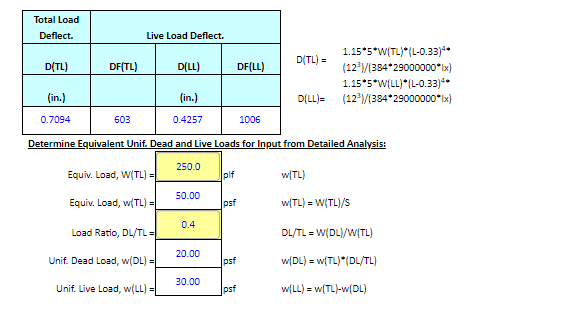
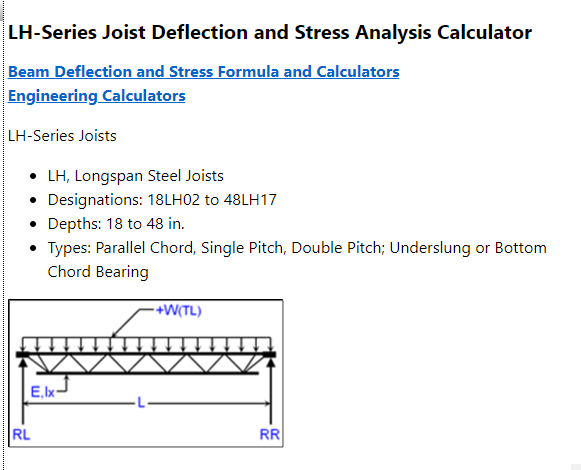

Design Basis:
Designs shall be made according to the provisions in this Specification for either; Load and Resistance Factor Design (LRFD), or for Allowable Strength Design (ASD).
Load Combinations:
LRFD: When load combinations are not specified to the joist manufacturer, the required stress shall be computed for the factored loads based on the factors and load combinations as follows:
1.4D
1.2D + 1.6 ( L, or Lr, or S, or R )
ASD: When load combinations are not specified to the joist manufacturer, the required stress shall be computed based on the load combinations as follows:
D
D + ( L, or Lr, or S, or R )
Where:
D = dead load due to the weight of the structural elements and the permanent features of the structure
L = live load due to occupancy and movable equipment
Lr = roof live load
S = snow load
R = load due to initial rainwater or ice exclusive of the ponding contribution
When special loads are specified and the specifying professional does not provide the load combinations, the provisions of ASCE 7, “Minimum Design Loads for Buildings and Other Structures” shall be used for LRFD and ASD load combinations.
1003.2 DESIGN AND ALLOWABLE STRESSES
Design Using Load and Resistance Factor Design (LRFD)
Joist Girders shall have their components so proportioned that the required stresses, fu, shall not exceed fFn where,
fu = required stress ksi (MPa)
Fn = nominal stress ksi (MPa)
f= resistance factor
fFn = design stress
Design Using Allowable Strength Design (ASD)
Joist Girders shall have their components so proportioned that the required stresses, f, shall not exceed Fn/W
where,
f = required stress ksi (MPa)
Fn = nominal stress ksi (MPa)
W= safety factor
Fn/W= allowable stress
Stresses:
(a) Tension: ft = 0.90 (LRFD) Wt = 1.67 (ASD)
For Chords: Fy = 50 ksi (345 MPa)
For Webs: Fy = 50 ksi (345 MPa), or Fy = 36 ksi (250 MPa)
Design Stress = 0.9Fy (LRFD) (1003.2-1)
Allowable Stress = 0.6Fy (ASD) (1003.2-2)
(b) Compression: fc = 0.90 (LRFD) Wc = 1.67 (ASD)

Where Fe = Elastic bucking stress determined in accordance with Equation 1003.2-5.
For hot-rolled sections, “Q” is the full reduction factor for slender compression elements.
Design Stress = 0.9 Fcr (LRFD) (1003.2-6)
Allowable Stress = 0.6 Fcr (ASD) (1003.2-7)
i. In the above equations, l is taken as the distance, in inches (millimeters), between panel points for the chord members and the appropriate length for web members, and r is the corresponding least radius of gyration of the member or any component thereof. E is equal to 29,000 ksi (200,000 MPa).
ii. Use 1.2 l/rx for a crimped, first primary compression web member when a moment-resistant weld group is not used for this member; where rx = member radius of gyration in the plane of the joist.
iii. For cold-formed sections, the method of calculating the nominal column strength is given in the AISI, North American Specification for the Design of Cold-Formed Steel Structural Members.
(c) Bending: fb = 0.90 (LRFD) Wb = 1.67 (ASD)
Bending calculations are to be based on using the elastic section modulus.
1- For chords and web members other than solid rounds:
Fy = 50 ksi (345 MPa)
Design Stress = 0.90 Fy (LRFD) (1003.2-8)
Allowable Stress = 0.60 Fy (ASD) (1003.2-9)
2- For web members of solid round cross section:
Fy = 50 ksi (345 MPa), or Fy = 36 ksi (250 MPa)
Design Stress = 1.45 Fy (LRFD) (1003.2-10)
Allowable Stress = 0.95 Fy (ASD) (1003.2-11)
3- For bearing plates:
Fy = 50 ksi (345 MPa), or Fy = 36 ksi (250 MPa)
Design Stress = 1.35 Fy (LRFD) (1003.2-12)
Allowable Stress = 0.90 Fy (ASD) (1003.2-13)
(d) Weld Strength:
Shear at throat of fillet welds:
Nominal Shear Stress = Fnw = 0.6Fexx (1003.2-14)
LRFD: fw = 0.75
Design Shear Strength = fRn = fwFnw A = 0.45Fexx A (1003.2-15)
ASD: Ww = 2.0
Allowable Shear Strength = (1003.2-16)
Rn /Ww = FnwA/Ww = 0.3Fexx A
A = effective throat area
Made with E70 series electrodes or F7XX-EXXX fluxelectrode combinations:
Fexx = 70 ksi (483 MPa)
Made with E60 series electrodes or F6XX-EXXX fluxelectrode combinations:
Fexx = 60 ksi (414 MPa)
Tension or compression on groove or butt welds shall be the same as those specified for the connected material.
1003.3 MAXIMUM SLENDERNESS RATIOS
The slenderness ratio l/r, where l is the length center-to center of support points and r is the corresponding least radius of gyration, shall not exceed the following:
Top chord end panels . . . . . . . . . . . . . . . . . . . . . . . . . . . . . . . . . . . . . . . 90
Top chord end panels . . . . . . . . . . . . . . . . . . . . . . . . . . . . . . . . . . . . . . . 120
Compression members other than top chord . . . . . . ………………… . . . 200
Tension members . . . . . . . . . . . . . . . . . . . . . . . . . . . . . . . . . . . . . . . . . . . . 240
1003.4 MEMBERS
(a) Chords
i. The bottom chord shall be designed as an axially loaded tension member. The radius of gyration of the bottom chord about its vertical axis shall not be less than l/240 where l is the distance between lines of bracing.
ii. The top chord shall be designed as an axial loaded compression member. The radius of gyration of the top chord about the vertical axis shall not be less than Span/575.
iii. The top chord shall be considered as stayed laterally by the steel joists provided positive attachment is made.
(b) Web
i. The vertical shears to be used in the design of the web members shall be determined from full loading, but such vertical shear shall be not less than 25 percent of the end reaction.
ii. Interior vertical web members used in modified Warren type web systems that do not support the direct loads through steel joists shall be designed to resist an axial load of 2 percent of the top chord axial force.
iii. Tension members shall be designed to resist at least 25 percent of their axial force in compression.
(c) Fillers and Ties
In compression members composed of two components, when fillers, ties or welds are used, they shall be spaced so the l/r ratio for each component does not exceed the l/r ratio of the member as a whole. In tension members composed of two components, when fillers, ties or welds are used, they shall be spaced so that the l/r ratio of each component does not exceed 240. The least radius of gyration shall be used in computing the l/r ratio of a component.
(d) Eccentricity
Members connected at a joint shall have their center of gravity lines meet at a point, if practical. Eccentricity on either side of the centroid of chord members may be neglected when it does not exceed the distance between the centroid and the back of the chord. Otherwise, provision shall be made for the stresses due to eccentricity. Ends of Joist Girders shall be proportioned to resist bending produced by eccentricity at the support. In those cases where a single angle compression member is attached to the outside of the stem of a tee or double angle chord, due consideration shall be given to eccentricity.
(e) Extended Ends
Extended top chords or full depth cantilever ends require the special attention of the specifying professional. The magnitude and location of the loads to be supported, deflection requirements, and proper bracing shall be clearly indicated on the structural drawings.
1003.5 CONNECTIONS
(a) Methods
Joint connections and splices shall be made by attaching the members to one another by arc or resistance welding or other accredited methods.
(1) Welded Connections
a) Selected welds shall be inspected visually by the manufacturer. Prior to this inspection, weld slag shall be removed.
b) Cracks are not acceptable and shall be repaired.
c) Thorough fusion shall exist between layers of weld metal and between weld metal and base metal for the required design length of the weld; such fusion shall be verified by visual inspection.
d) Unfilled weld craters shall not be included in the design length of the weld.
e) Undercut shall not exceed 1/16 inch (2 millimeters) for welds oriented parallel to the principal stress.
f) The sum of surface (piping) porosity diameters shall not exceed 1/16 inch (2 millimeters) in any 1 inch (25 millimeters) of design weld length.
g) Weld spatter that does not interfere with paint coverage is acceptable.
(2) Welding Program
Manufacturers shall have a program for establishing weld procedures and operator qualification, and for weld sampling and testing.
(3) Weld Inspection by Outside Agencies (See Section 1004.10 of this specification).
The agency shall arrange for visual inspection to determine that welds meet the acceptance standards of Section 1003.5(a)(1). Ultrasonic, X-Ray, and magnetic particle testing are inappropriate for Joists Girders due to the configurations of the components and welds.
(b) Strength
(1) Joint Connections – Joint connections shall develop the maximum force due to any of the design loads, but not less than 50 percent of the strength of the member in tension or compression, whichever force is the controlling factor in the selection of the member.
(2) Shop Splices - Shop splices may occur at any point in chord or web members. Splices shall be designed for the member force but not less than 50 percent of the member strength. Members containing a butt weld splice shall develop an ultimate tensile force of at least 57 ksi (393 MPa) times the full design area of the chord or web. The term “member” shall be defined as all component parts comprising the chord or web, at the point of splice.
(c) Field Splices
Field Splices shall be designed by the manufacturer and may be either bolted or welded. Splices shall be designed for the member force, but not less than 50 percent of the member strength.
1003.6 CAMBER
Joist Girders shall have approximate cambers in accordance with the following:
TABLE 1003.6-1
Top Chord Length Approximate Camber
------------------------- ------------------------------
20'-0" (6096 mm) 1/4" (6 mm)
30'-0" (9144 mm) 3/8" (10 mm)
40'-0" (12192 mm) 5/8" (16 mm)
50'-0" (15240 mm) 1" (25 mm)
60'-0" (18288 mm) 1 1/2" (38 mm)
70'-0" (21336 mm) 2" (51 mm)
80'-0" (24384 mm) 2 3/4" (70 mm)
90'-0" (27342 mm) 3 1/2" (89 mm)
100'-0" (30480 mm) 4 1/4" (108 mm)
110'-0" (33528 mm) 5" (127 mm)
120'-0" (36576 mm) 6" (152 mm)
The specifying professional shall give consideration to coordinating Joist Girder camber with adjacent framing.
1003.7 VERIFICATION OF DESIGN AND MANUFACTURE
(a) Design Calculations
Companies manufacturing Joist Girders shall submit design data to the Steel Joist Institute (or an independent agency approved by the Steel Joist Institute) for verification of compliance with the SJI Specifications.
(b) In-Plant Inspections
Each manufacturer shall verify their ability to manufacture Joist Girders through periodic In-Plant Inspections. Inspections shall be performed by an independent agency approved by the Steel Joist Institute. The frequency, manner of inspection, and manner of reporting shall be determined by the Steel Joist Institute. The In-Plant Inspections are not a guarantee of the quality of any specific Joist Girder; this responsibility lies fully and solely with the individual manufacturer.
SECTION 1004-APPLICATION
1004.1 USAGE
This specification shall apply to any type of structure where steel joists are to be supported directly by Joist Girders installed as hereinafter specified. Where Joist Girders are used other than on simple spans under equal concentrated gravity loading, as prescribed in Section 1003.1, they shall be investigated and modified if necessary to limit the unit stresses to those listed in Section 1003.2. The magnitude and location of all loads and forces, other than equal concentrated gravity loading, shall be provided on the structural drawings. The specifying professional shall design the supporting structure, including the design of columns, connections, and moment plates*.
This design shall account for the stresses caused by lateral forces and the stresses due to connecting the bottom chord to the column or other support. The designed detail of a rigid type connection and moment plates shall be shown on the structural drawings by the specifying professional. The moment plates shall be furnished by other than the joist manufacturer.
* For further reference, refer to Steel Joist Institute Technical Digest #11, “Design of Joist-Girder Frames”
1004.2 SPAN
The span of a Joist Girder shall not exceed 24 times its depth.
1004.3 DEPTH
Joist Girders may have either parallel top chords or a top chord slope of 1/8 inch per foot (1:96). The nominal depth of sloping chord Joist Girders shall be the depth at mid-span.
1004.4 END SUPPORTS
(A) Masonry and Concrete
Joist Girders supported by masonry or concrete are to bear on steel bearing plates and shall be designed as steel bearing.
Due consideration of the end reactions and all other vertical and lateral forces shall be taken by the specifying professional in the design of the steel bearing plate and the masonry or concrete. The ends of Joist Girders shall extend a distance of not less than 6 inches (152 millimeters) over the masonry or concrete support and be anchored to the steel bearing plate. The plate shall be located not more than 1/2 inch (13 millimeters) from the face of the wall and shall be not less than 9 inches (229 millimeters) wide perpendicular to the length of the girder. The plate is to be designed by the specifying professional and shall be furnished by other than the joist manufacturer.
Where it is deemed necessary to bear less than 6 inches (152 millimeters) over the masonry or concrete support, special consideration is to be given to the design of the steel bearing plate and the masonry or concrete by the specifying professional. The girders must bear a minimum of 4 inches (102 millimeters) on the steel bearing plate.
(B) Steel
Due consideration of the end reactions and all other vertical and lateral forces shall be taken by the specifying professional in the design of the steel support. The ends of Joist Girders shall extend a distance of not less than 4 inches (102 millimeters) over the steel supports and shall have positive attachment to the support, either by bolting or welding.
1004.5 BRACING
Joist Girders shall be proportioned such that they can be erected without bridging (See Section 1004.9 for bracing required for uplift forces). Therefore, the following requirements must be met:
a) The ends of the bottom chord are restrained from lateral movement to brace the girder from overturning. For Joist Girders at columns in steel frames, restraint shall be provided by a stabilizer plate on the column.
b) No other loads shall be placed on the Joist Girder until the steel joists bearing on the girder are in place and welded to the girder.
1004.6 END ANCHORAGE
(A) Masonry and Concrete
Ends of Joist Girders resting on steel bearing plates on masonry or structural concrete shall be attached thereto with a minimum of two 1/4 inch (6 millimeters) fillet welds 2 inches (51 millimeters) long, or with two 3/4 inch (19 millimeters) bolts, or the equivalent.
(B) Steel
Ends of Joist Girders resting on steel supports shall be attached thereto with a minimum of two 1/4 inch (6 millimeters) fillet welds 2 inches (51 millimeters) long, or with two 3/4 inch (19 millimeters) bolts, or the equivalent. In steel frames, bearing seats for Joist Girders shall be fabricated to allow for field bolting.
(C) Uplift
Where uplift forces are a design consideration, roof Joist Girders shall be anchored to resist such forces (Refer to Section 1004.9).
1004.7 DEFLECTION
The deflections due to the design live load shall not exceed the following:
I. Floors: 1/360 of span.
II. Roofs: 1/360 of span; where a plaster ceiling is attached or suspended.
III. 1/240 of span for all other cases.
The specifying professional shall give consideration to the effects of deflection and vibration* in the selection of Joist Girders.* For further reference, refer to Steel Joist Institute Technical Digest #5, “Vibration of Steel Joist-Concrete Slab Floors” and the Institute’s Computer Vibration Program.
1004.8 PONDING*
The ponding investigation shall be performed by the specifying professional. * For further reference, refer to Steel Joist Institute Technical Digest #3, “Structural Design of Steel Joist Roofs to Resist Ponding Loads” and AISC Specifications.
1004.9 UPLIFT
Where uplift forces due to wind are a design requirement, these forces must be indicated on the contract drawings in terms of NET uplift in pounds per square foot (Pascals). The contract drawings must indicate if the net uplift is based on ASD or LRFD. When these forces are specified, they must be considered in the design of Joist Girders and/or bracing.
If the ends of the bottom chord are not strutted, bracing must be provided near the first bottom chord panel points whenever uplift due to wind forces is a design consideration.* * For further reference, refer to Steel Joist Institute Technical Digest #6, “Structural Design of Steel Joist Roofs to Resist Uplift Loads”.
1004.10 INSPECTION
Joist Girders shall be inspected by the manufacturer before shipment to verify compliance of materials and workmanship with the requirements of this specification. If the purchaser wishes an inspection of the Joist Girders by someone other than the manufacturer’s own inspectors, they may reserve the right to do so in their “Invitation to Bid” or the accompanying “Job Specifications”. Arrangements shall be made with the manufacturer for such inspection of the Joist Girders at the manufacturing shop by the purchaser’s inspectors at purchaser’s expense.
SECTION 1005-HANDLING AND ERECTION
Particular attention should be paid to the erection of Joist Girders. Care shall be exercised at all times to avoid damage through careless handling during unloading, storing and erecting. Dropping of Joist Girders shall not be permitted. In steel framing, where Joist Girders are utilized at column lines, the Joist Girder shall be field-bolted at the column. Before hoisting cables are released and before an employee is allowed on the Joist Girder the following conditions must be met:
a) The seat at each end of the Joist Girder is attached in accordance with Section 1004.6. When a bolted seat connection is used for erection purposes, as a minimum, the bolts must be snug tightened. The snug tight condition is defined as the tightness that exists when all plies of a joint are in firm contact. This may be attained by a few impacts of an impact wrench or the full effort of an employee using an ordinary spud wrench.
b) Where stabilizer plates are required the Joist Girder bottom chord must engage the stabilizer plate. During the construction period, the contractor shall provide means for the adequate distribution of loads so that the carrying capacity of any Joist Girder is not exceeded.
Joist Girders shall not be used as anchorage points for a fall arrest system unless written direction to do so is obtained from a “qualified person”.(1) Field welding shall not damage the Joist Girder. The total length of weld at any one cross-section on cold-formed members whose yield strength has been attained by cold working and whose as-formed strength is used in the design, shall not exceed 50 percent of the overall developed width of the cold-formed section. * For a thorough coverage of this topic, refer to SJI Technical Digest #9, “Handling and Erection of Steel Joists and Joist Girders”. (1) See Appendix E for OSHA definition of “qualified person”.
SECTION 1006-HOW TO SPECIFY JOIST GIRDERS
For a given Joist Girder span, the specifying professional first determines the number of joist spaces. Then the panel point loads are calculated and a depth is selected. The following tables give the Joist Girder weight in pounds per linear foot (kilo-Newton per meter) for various depths and loads.
1. The purpose of the Joist Girder Design Guide Weight Table is to assist the specifying professional in the selection of a roof or floor support system.
2. It is not necessary to use only the depths, spans, or loads shown in the tables.
3. Holes in chord elements present special problems which must be considered by both the specifying professional and the Joist Girder Manufacturer. The sizes and locations of such holes shall be clearly indicated on the structural drawings.
When dealing with steel joists and their spans, a few thumb rules can help guide design and ensure structural adequacy. These rules are general guidelines and should always be verified by detailed calculations and professional engineering advice. Here are some common thumb rules for steel joist spans:
Span-to-Depth Ratio: For steel joists, a typical span-to-depth ratio is around 20:1. This means that the span (distance between supports) should be approximately 20 times the depth of the joist. For example, if the depth of the joist is 12 inches, the span would be approximately 240 inches (or 20 feet).
Joist Spacing: Common spacing for steel joists is 24 inches on center. However, depending on the load and design requirements, spacing can vary, typically ranging from 16 to 24 inches on center.
Maximum Span for Typical Loads: For light to moderate loads, typical span ranges for steel joists can be up to 40 feet. For more demanding loads or specific design criteria, this span may be reduced.
Load Capacity Considerations: The load capacity of steel joists is influenced by factors such as the type of steel used, the size and shape of the joist, and the load distribution. Ensure that the joist design complies with local building codes and standards.
Deflection Limits: Deflection limits are critical for ensuring structural performance and comfort. A common thumb rule for deflection is that the maximum deflection should not exceed L/240 of the span, where L is the span length. For more critical applications, tighter deflection limits may be required.
Load Distribution: Ensure that the loads are evenly distributed across the joists to prevent localized overstressing. In cases of irregular loads or concentrated loads, additional design considerations may be needed.
These thumb rules provide a starting point, but each project will have unique requirements that might necessitate adjustments. Always consult with a structural engineer to ensure that the design meets safety standards and codes.
When dealing with steel joists and their spans, a few thumb rules can help guide design and ensure structural adequacy. These rules are general guidelines and should always be verified by detailed calculations and professional engineering advice. Here are some common thumb rules for steel joist spans:
Span-to-Depth Ratio: For steel joists, a typical span-to-depth ratio is around 20:1. This means that the span (distance between supports) should be approximately 20 times the depth of the joist. For example, if the depth of the joist is 12 inches, the span would be approximately 240 inches (or 20 feet).
Joist Spacing: Common spacing for steel joists is 24 inches on center. However, depending on the load and design requirements, spacing can vary, typically ranging from 16 to 24 inches on center.
Maximum Span for Typical Loads: For light to moderate loads, typical span ranges for steel joists can be up to 40 feet. For more demanding loads or specific design criteria, this span may be reduced.
Load Capacity Considerations: The load capacity of steel joists is influenced by factors such as the type of steel used, the size and shape of the joist, and the load distribution. Ensure that the joist design complies with local building codes and standards.
Deflection Limits: Deflection limits are critical for ensuring structural performance and comfort. A common thumb rule for deflection is that the maximum deflection should not exceed L/240 of the span, where L is the span length. For more critical applications, tighter deflection limits may be required.
Load Distribution: Ensure that the loads are evenly distributed across the joists to prevent localized overstressing. In cases of irregular loads or concentrated loads, additional design considerations may be needed.
These thumb rules provide a starting point, but each project will have unique requirements that might necessitate adjustments. Always consult with a structural engineer to ensure that the design meets safety standards and codes.
Designing joists involves several key steps to ensure they are structurally sound and meet building codes. Here’s a basic outline of the process:
1. Determine Load Requirements
Dead Load: Weight of the building materials and any fixed components.
Live Load: Weight of movable objects and people.
Environmental Loads: Snow, wind, and seismic forces if applicable.
2. Select Joist Type
Solid Wood Joists: Traditional and often used in residential buildings.
Engineered Wood Joists (I-joists): Pre-manufactured for greater strength and uniformity.
Steel Joists: Used for heavier loads or longer spans.
3. Calculate Joist Span and Spacing
Determine the span (distance between supports) and spacing based on load requirements and the type of joist selected. Building codes provide guidelines for these calculations.
4. Choose Joist Dimensions
For wood joists, select the appropriate size (depth and width) based on span and load requirements. For engineered joists, refer to the manufacturer's specifications.
5. Check for Deflection
Ensure the joists do not bend excessively under load. Deflection limits are specified by building codes and depend on the span and load.
6. Consider Bearing and Supports
Determine how joists will be supported at their ends and along their length. Ensure that bearing areas are sufficient and that supports are properly designed.
7. Review Building Codes
Verify that your design complies with local building codes and standards. Codes will dictate minimum requirements for load capacity, spacing, and deflection.
8. Detail Joist Connections
Design connections for joists to beams, walls, and other structural elements. This includes selecting appropriate hangers, fasteners, or other hardware.
9. Perform Structural Analysis
Use structural analysis methods or software to verify that the joists will perform as expected under the applied loads.
10. Document the Design
Prepare detailed drawings and specifications for construction, including dimensions, materials, load capacities, and installation instructions.
11. Review and Revise
Have the design reviewed by a structural engineer or another qualified professional to ensure accuracy and safety.
12. Consider Installation Details
Plan for any site-specific factors, such as access for installation and integration with other building elements.
By following these steps, you can ensure that your joist design is both functional and compliant with safety standards.
To find how far any particular size of floor joist can span, we need to combine two formulas for the vertical deflection, δδ. The first deflection formula we need determines the allowable sag of a floor joist using a ratio. According to the 2012 International Building Code, the sag or deflection of a floor joist subjected to dead and live loads should not exceed a measurement equal to the span of the floor joist, L (in inches), divided by 240240. In equation form, we express that as:
δ=L/240δ=L/240
We can also divide LL by 360360, 480480, 600600, or 720720, depending on what loading combination you wish to consider in your calculation or how much deflection you want to allow. As a rule of thumb, we use 240240 for a combination of dead and live loads our floor will have to carry.
We then simultaneously use that equation with this maximum allowable deflection formula based on the floor joist material composition, its cross-section, and the load it supports
4
Deflection = 5WL /384EI
-------------------------------------------------
here:
δδ is the maximum allowable deflection of floor joists;
uu is the uniformly distributed load a floor joist will carry;
LL is the span of the floor joist;
EE is the modulus of elasticity; and
II is the area moment of inertia.
· If you know the load that your floor will carry (say PP in terms of force per unit area), you have to multiply it by the on-center spacing (ss) that you plan for your joists to get its equivalent uniform distributed load along the joists:
· u=P×su=P×s · For the modulus of elasticity, you can refer to this table from the American Wood
We calculate the area moment of inertia using this formula:
3
I=w×h /12
where:
II is the area moment of inertia;
w is the actual width of floor joist; and
h is the actual height of floor joist.
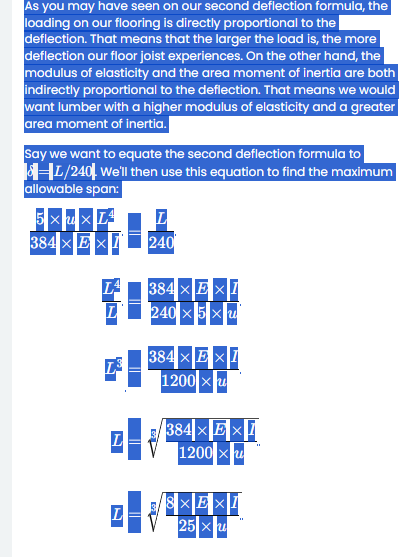
To calculate how many floor joists you will need, let's say on a floor that is 10 feet (or 120 inches) long and using 1.5-inch thick floor joists at 16 inches on-center spacing:
Subtract the width of your floor joist from your floor's length:
120" − 1.5" = 118.5"
Divide that difference by the sum of the on-center spacing of the floor joists:
118.5" / 16" = 7.40625
Add 1 to this value and round up the answer to the next whole number:
7.40625 + 1 = 8.40625 ≈ 9 floor joists
Comments